Noticias
Por Periodista , 18 de julio de 2017Cómo replicar en la minería chilena la experiencia del túnel más largo del mundo
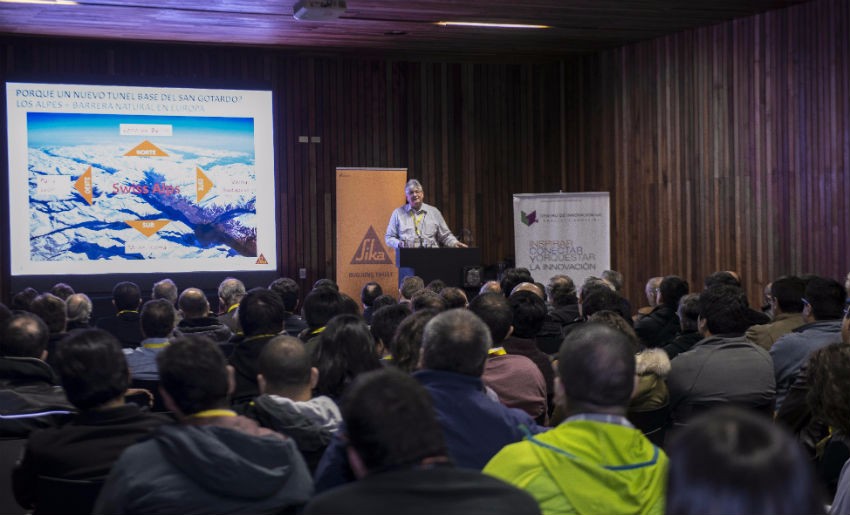
El túnel San Gotardo que une a Zürich con Milán en poco más de 2 horas, bajo los Alpes, es el más largo del mundo. Mide 57,1 kilómetros, y fue concretado tras 17 años de construcción y múltiples investigaciones para lograr los materiales que garantizaran los 100 años de durabilidad exigidos por el mandante.
Actor protagónico en esta construcción es el ingeniero Ernesto Schümperli, quien relató la experiencia ante un auditorio de más de 160 personas, entre ingenieros, contratistas de obras viales, gerentes de empresas mineras y de tecnologías de la construcción reunidos en la Universidad Católica.
Este caso cobra especial interés en Chile, debido al impacto del túnel suizo como referente para la infraestructura subterránea en obras viales, como el Metro de Santiago; mineras, como el proyecto Chuquicamata, y de energía, donde Sika está aplicando las tecnologías usadas en San Gotardo.
Al respecto, el Gerente General de Sika, Juan Francisco Jiménez, sostiene que la geología y los terremotos en Chile marcan una diferencia importante para enfrentar obras de tunelería de esta envergadura, pero que podemos sacar lecciones importantes. "La experiencia, el conocimiento en Chile lo tenemos. Pero nos faltan dos cosas: cumplir con los plazos y costos y, en segundo lugar, no caer en la tentación de ahorrar costos dejando para el final de la obra los sondeos y pruebas necesarias al inicio del proyecto".
DESAFÍO DE MARCA MAYOR
Schümperli, presidente de Infraestructura y Minería de Sika global, explicó que la construcción del túnel representó un desafío de marca mayor, partiendo por los 6 años de investigaciones y prueba de materiales que debió cumplir la empresa para garantizar no sólo la calidad de la megaestructura, sino también que la geología bajo el macizo alpino resistiría las faenas.
Además de los múltiples ensayos, los ingenieros se encontraron con el problema del estallido de las rocas mientras iban excavando y el efecto de los sismos que derribaban lo avanzado el día anterior. "Hubo que tomar muchas decisiones de diseño, como por ejemplo separar el túnel en dos para las dos direcciones en que pasarían los trenes, como una medida de seguridad necesaria, que no estaba en la planificación original o cambiar de planes in situ por las deformaciones que iban sufriendo los avances debido a la alta presión de la montaña sobre la obra".
Añade que "durante los ensayos, pensábamos que muchas de las exigencias eran una locura, que eran cosas imposibles de alcanzar, como retardar y acelerar al mismo tiempo un hormigón. Hubo que inventar nuevos productos que respondieran a estas demandas, hicimos ensayos con muchos tipos distintos de cementos, cientos de mezclas que se fueron descartando. Y finalmente sí fuimos resolviendo cada obstáculo gracias a un gran equipo de profesionales, fundamental para alcanzar los objetivos y superar los obstáculos diarios en la impermeabilización de los túneles", explica Schümperli.
COMENTA AQUÍ